How to Use Plastic Advisor in Pro/Engineer?
Introduction
The Adviser is designed to help an engineer determine the manufacturability of plastic part designs.
Cavity models
The Adviser allows you to create a model of your part in a CAD package, and then read the model in to the Adviser.
Analysis preparations
For a Plastic Flow analysis, you need to select the polymer and the injection location. Other settings, such as material temperature and pressure, are automatically selected according to the material’s properties, but you can alter them if you wish.
Additional analyses can also be performed in order to investigate other aspects of part design.
Ok, this is an example of using plastic advisor at upper case of charger for NOKIA. Before you try to analyze a model, I hope you should be understand about designing plastic product, including how to creating rib, how about draft angle, Round Corner, Thickness and other criteria for plastic design.
Step bye Step to Run Plastic Adviser.
Ok, this is the step by step using Plastic Adviser within Pro/Engineer. Enjoy it…
The first Requirements to run Plastic Adviser are built a model as Cavity. If you have finished your plastic model, you can run Plastic Adviser with the following some ways:
- Click Application in Menu Bar and then choose Plastic Adviser -> middle click to ignore set injection location in order to determining best injection location in plastic adviser Windows that will appear for a few minutes after you click on middle button.

- After Plastic Adviser Windows was appear, you must set Molding Parameters Such as Material Type, Material Operating Temperature, Mold Temperature, Injection Pressure by click Adviser on Menu Bar and choose molding parameter, and then molding parameters dialog will be appear. For Select Material, you must set plastic manufacturer and choose your material. And then set mold temperature and Injection Pressure in Processing Condition Tab. In this case, I try to use Bayer ABS Limited as Manufacturer and Absolac 300 As trade name with Mold Temperature (60oC), Melt Temp (225 oC), Injection Pressure( 250Mpa), Machine Clamp Open Time (3 sec). See this Picture.
- Set Injection Location, Please Determine the best location for placement gate. Click Adviser and choose Pick Injection Location and then click where you want to set best location for gate in the cavity model.
- Run Analysis; you can select type of analysis based on your needed bye click Adviser -> click Analysis Selection and Then you add check list for type an analysis. This is checking for flow analysis.

- Result.

- You can read result under result menu bar and then you can show type of analysis result. This is sample Pressure drop result.
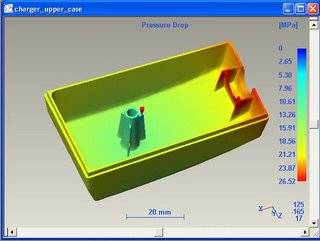
Sample Result : Preswsure Drop
- You can view analysis type and solving problem if there are some bad characteristic.
Results
After the Plastic Flow analysis has finished, you can look at the Confidence of Fill result, which is derived from the Fill Time, Injection Pressure, Pressure Drop and Flow Front Temperature results.
A green area has a high confidence rating yellow indicates a medium confidence rating, while red shows a low confidence rating.
Read the Confidence of Fill advice for suggestions on improving a medium or low result. If the Confidence of Fill result indicates problems, look at the other results to find the reason for the low or medium confidence of fill.
If the Confidence of Fill result shows any molding problems, look at the pressure and temperature results to identify where the problem is coming from. After looking at the Confidence of Fill, you should study the air trap and weld line results to find other possible molding problems.
You can then review the inputs and try to resolve any problems. Areas on the part that show low or medium confidence of fill may need to be redesigned or a new material selected for the part to fill.
Once you are confident that the part will fill, you can check the Quality Prediction result, which estimates the expected quality of the part's appearance. To find out more information and possible solutions to any implied problems, use the same methods you used for investigating the Confidence of Fill result. You can also use other analyses available to investigate and solve design problems.
Tutorial & Model by Ibrahim
0 comments:
Post a Comment